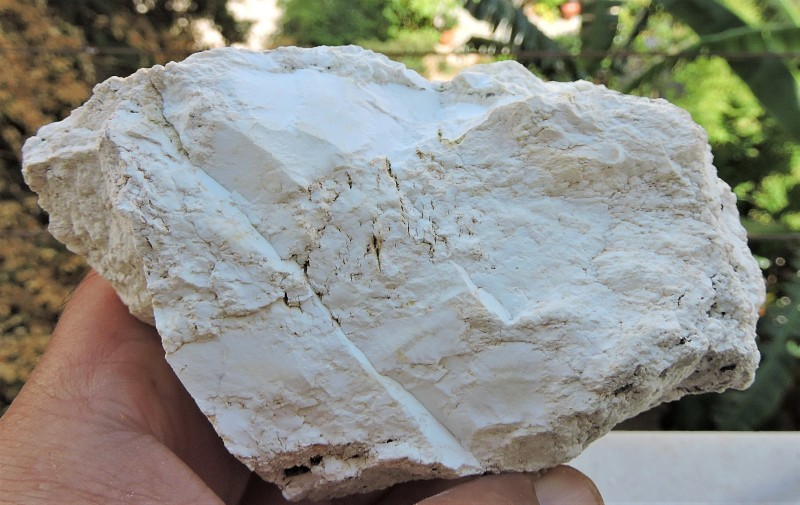
Magnesium
Capabilities
Raw Material Extraction and Beneficiation
Through collaborations with clients and partners worldwide, we have developed our knowledge and skills in extracting and enhancing carbonates, chlorides, and magnesium oxide ores.
Studies and Design Reviews
Having conducted more than 20 studies on lithium chemicals, we have successfully introduced the bicarbonation purification process for lithium carbonate in the lithium industry. This innovation has facilitated the precise production of high-purity battery-grade products, leading to enhanced sustainability in our clients' business operations.
Developing and designing front-end processes
For newcomers in the lithium industry, navigating the complexities can be challenging. Our expertise lies in providing comprehensive economic analyses, establishing industry connections, and meticulously planning and executing laboratory and pilot-plant trials to validate process flow sheets. Moreover, our environmental services play a crucial role in shaping project timelines by integrating permitting considerations early in the project development phase. Addressing aspects such as tailings disposal, pond design, and managing reagent-supply logistics are pivotal for ensuring the success of new ventures in the industry.
Process of Reduction
These methods involve subjecting oxides to high-temperature treatments with a reductant like silicon or aluminum, along with employing electrolytic processes commonly utilizing chlorides. Our extensive expertise encompasses both approaches and the diverse array of technologies within each category.
Melting Treatment and Casting
We possess extensive and up-to-date expertise in various casting technologies, including our proprietary advancements in direct chill casting. Tailoring solutions to align with the specific requirements of our clients' operations, we enhance value by integrating process, technology, and operational insights with a track record of successful project execution.
Plant Design
Securing capital poses a significant challenge for businesses of any scale. In order to cater to the needs of smaller capital-intensive plants ranging from $100 million to $600 million, we have honed our expertise in designing plants within the "sub-billion-dollar" range. Emphasizing quality classification of facilities at the project's inception, cost-efficiency remains a central theme throughout the design phase. A robust 3D layout and the selection of suitable construction materials play pivotal roles in ensuring project success..
Designing Processes for Downstream Plants
The downstream processing options available to our clients encompass strip production through ingot metallurgy or roll casting, forging, punch press forming, and utilization of both HPDC and LPDC processes.
Designing Utility and Off-Gas Handling Systems
Off-gas management holds paramount significance, particularly in electrolytic magnesium plants due to the toxicity and value of the byproduct. Our expertise encompasses designing effective chlorine off-gas handling systems along with solutions for handling other conventional gases.
Industry challenges
Magnesium is becoming increasingly intertwined with green technology as global awareness of environmental sustainability grows. This heightened consciousness has led to a surge in the demand for magnesium.
Notably, in emerging markets, the desire for more vehicles persists despite stricter emission regulations. This has spurred a competition to manufacture lighter, more fuel-efficient, and recyclable automobiles. Industry experts within the automotive sector advocate for magnesium as a promising material due to its lightweight nature, adaptability, and recyclability.
While magnesium boasts eco-friendly attributes, its environmental impact during primary production necessitates mitigation to strengthen its green credentials. To sway opinions in its favor, efforts should focus on reducing its greenhouse gas emissions in the manufacturing process. Simultaneously, exploring advancements in process technology and automation is crucial to drive down costs associated with bringing magnesium to the market.